ALN Ceramics
ALN Ceramics, or aluminum nitride ceramics, are advanced materials renowned for their exceptional thermal, mechanical, and electrical properties. As technology advances, the demand for materials that can withstand extreme conditions while providing reliable performance continues to grow. ALN ceramics have emerged as a preferred choice in various industries, including electronics, aerospace, and automotive, thanks to their unique attributes.
In this article, we will explore what ALN ceramics are, their properties, manufacturing processes, applications, advantages, challenges, and future trends.
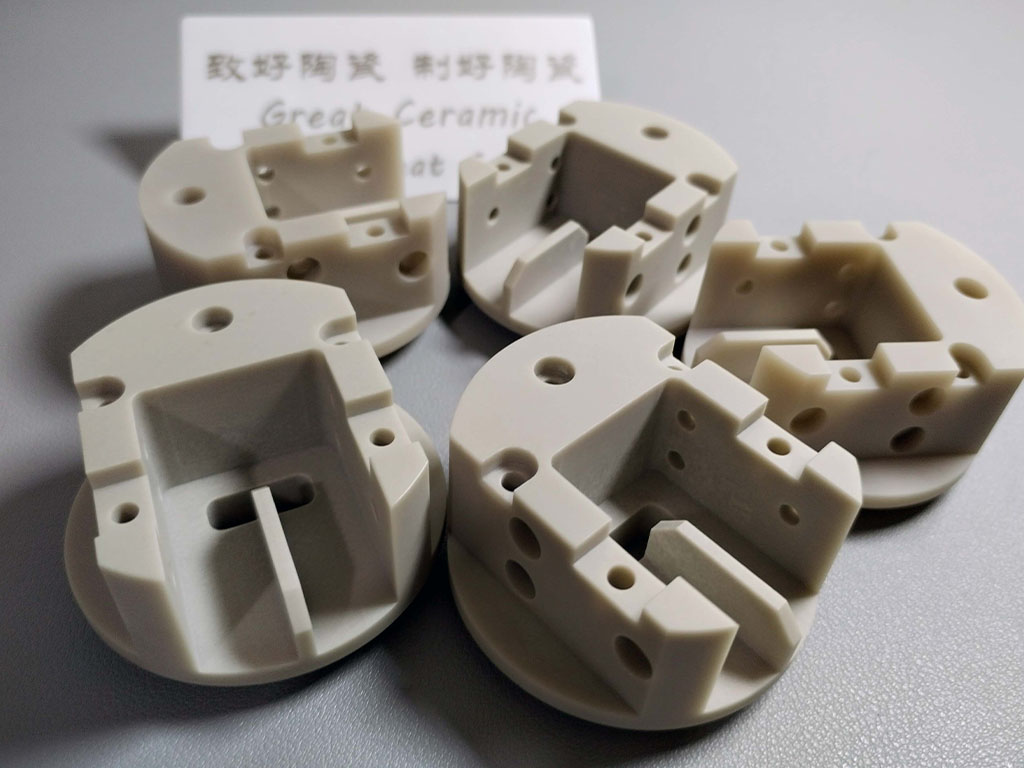
What is Aluminum Nitride?
Aluminum nitride (AlN) is a compound consisting of aluminum and nitrogen. It has gained significant attention since its development in the late 20th century due to its remarkable properties. Unlike traditional ceramics, which may exhibit brittleness or limited thermal conductivity, ALN ceramics stand out for their high thermal conductivity combined with excellent electrical insulation.
Historical Background
Aluminum nitride was first synthesized in the 1950s, but it wasn’t until the 1990s that its potential in industrial applications began to be fully realized. Owing to advancements in material science and manufacturing techniques, ALN ceramics have become increasingly viable for high-performance applications.
Comparison with Other Ceramic Materials
When compared to other ceramic materials such as alumina or silicon carbide, ALN ceramics offer superior thermal conductivity while maintaining excellent electrical insulating properties. This unique combination makes them ideal for applications where both thermal management and electrical insulation are crucial.
Properties of ALN Ceramics
Thermal Properties
One of the defining features of ALN ceramics is their high thermal conductivity, which can exceed >170 W/m·K. This property is critical in applications where efficient heat dissipation is necessary, such as in electronic devices and high-power equipment.
Thermal Expansion Coefficient: ALN exhibits a low coefficient of thermal expansion, which reduces the risk of thermal shock and ensures dimensional stability under varying temperatures.
Applications Benefiting from Thermal Properties: Industries such as electronics utilize ALN ceramics in heat sinks and substrates, where effective thermal management is vital for device longevity and performance.
Mechanical Properties
ALN ceramics are characterized by impressive mechanical strength and hardness. Their high wear resistance makes them suitable for demanding applications.
Hardness and Wear Resistance: The hardness of ALN ceramics rivals that of traditional hard materials, making them ideal for cutting tools and abrasive applications.
Strength and Brittleness: While they exhibit high strength, they can also be brittle, which is a common challenge in ceramic materials.
Implications for Engineering Applications: Understanding the mechanical properties of ALN is crucial for engineers designing components that must withstand mechanical stress while operating at high temperatures.
Electrical Properties
ALN ceramics are exceptional electrical insulators, which is vital for many electronic applications.
Insulating Properties: With a dielectric constant ranging from 8 to 9, ALN ceramics provide excellent insulation, making them suitable for high-voltage applications.
Dielectric Strength and Breakdown Voltage: The high dielectric strength allows ALN ceramics to perform well in environments where other materials might fail due to electrical breakdown.
Applications in Electronics and Semiconductor Industries: ALN is increasingly used in the manufacturing of substrates for LED technology and other semiconductor devices.
Chemical Stability
ALN ceramics exhibit remarkable chemical stability, making them resistant to oxidation and corrosion.
Resistance to Oxidation and Corrosion: This property allows ALN to be used in chemically aggressive environments without significant degradation.
Importance in Chemical Processing Industries: In sectors like petrochemicals and pharmaceuticals, ALN ceramics contribute to equipment durability and reliability.
Manufacturing Processes of ALN Ceramics
Powder Processing Techniques
The production of Aluminum Nitride ceramics typically involves several powder processing techniques that influence the final properties of the material.
Overview of Powder Preparation: Aluminum and nitrogen sources are carefully mixed and processed to create fine powders suitable for sintering.
Sintering Processes and Their Effects on Properties: Different sintering methods, including traditional and reactive sintering, can affect the density, microstructure, and mechanical properties of the final product.
Advanced Techniques: Innovations such as hot pressing and spark plasma sintering are being explored to enhance the properties of ALN ceramics, allowing for finer control over microstructure and performance.
Additive Manufacturing
The advent of 3D printing technologies has opened new avenues for Aluminum Nitride ceramics.
Benefits of 3D Printing with Aluminum Nitride: Additive manufacturing allows for complex geometries and designs that traditional manufacturing methods cannot achieve.
Case Studies of Successful Applications: Various industries are now exploring the use of 3D-printed Aluminum Nitride components for applications ranging from aerospace to healthcare.
Applications of ALN Ceramics
Aluminum Nitride ceramics are used in diverse applications due to their unique properties:
Electronics and Semiconductors
ALN ceramics are crucial in the electronics sector for several reasons.
Use in Heat Sinks and Substrates: Their high thermal conductivity allows them to efficiently dissipate heat, making them ideal for high-power electronic devices.
Role in High-Power Devices: Many modern electronics require materials that can handle increased thermal loads without compromising electrical insulation.
Aerospace Industry
In aerospace, ALN ceramics are valued for their lightweight and thermal management properties.
Applications in Thermal Management: Components made from ALN can withstand extreme temperatures while providing thermal stability, critical for aerospace applications.
Benefits in Lightweight Structures: The low density of Aluminum Nitride ceramics helps in reducing overall aircraft weight, leading to improved fuel efficiency.
Medical Applications
ALN ceramics are increasingly finding applications in the medical field.
Use in Dental Ceramics: Their biocompatibility and strength make them suitable for dental applications, including crowns and bridges.
Applications in Biomedical Devices: ALN ceramics are being explored for use in various medical devices due to their stability and durability.
Energy Sector
The energy sector also benefits from the properties of Aluminum Nitride ceramics.
Role in Energy-Efficient Devices: Aluminum Nitride ceramics contribute to the development of energy-efficient components in electrical systems.
Applications in Renewable Energy Technologies: Their thermal and electrical properties are being leveraged in solar cells and energy storage devices.
Automotive Industry
The automotive industry has seen increased interest in ALN ceramics.
Use in High-Temperature Applications: Aluminum Nitride components can withstand high temperatures and harsh environments, making them ideal for automotive applications.
Benefits for Performance and Durability: The robust nature of Aluminum Nitride ceramics helps improve the reliability and performance of automotive components.
Advantages of ALN Ceramics
Aluminum Nitride ceramics offer numerous advantages that make them a preferred choice in various applications.
Summary of Key Benefits: High thermal conductivity, excellent electrical insulation, and chemical stability are some of the standout features.
Comparison with Other Materials: When compared to alumina or silicon carbide, Aluminum Nitride ceramics often provide superior performance in thermal management applications.
Cost-Effectiveness and Longevity: Despite a higher initial cost, the longevity and reliability of Aluminum Nitride ceramics can lead to cost savings over time.
Future Trends in AlN Ceramics
The future of Aluminum Nitride ceramics looks promising as research continues to uncover new applications and enhancements.
Research and Development Directions: Innovations in processing methods and formulations will likely lead to even better performance characteristics.
Emerging Applications: As industries increasingly prioritize energy efficiency and durability, Aluminum Nitride ceramics will play a crucial role in developing next-generation materials.
Predictions for Market Growth and Technology Advancements: The global market for Aluminum Nitride ceramics is expected to grow significantly as demand increases for high-performance materials in various sectors.
Conclusion
Aluminum Nitride Ceramics represent a significant advancement in material science, offering a unique combination of properties that make them suitable for a wide range of applications. As industries continue to evolve and the demand for high-performance materials grows, aluminum nitride ceramics will play an essential role in shaping the future of technology.
Understanding the properties, applications, and challenges associated with Aluminum Nitride ceramics is crucial for engineers and decision-makers looking to leverage these advanced materials for innovative solutions.