Thermal Shock Resistance in Advanced Ceramics
Thermal shock resistance refers to a material's ability to withstand rapid changes in temperature without cracking or failing. Advanced ceramics, while known for their hardness and strength, can be vulnerable to sudden temperature shifts due to their inherent brittleness and low thermal expansion tolerance. This makes thermal shock resistance a key metric when selecting ceramics for high-temperature and high-stress environments.
Skip to
Data | Comparison | Applications | FAQs | Related
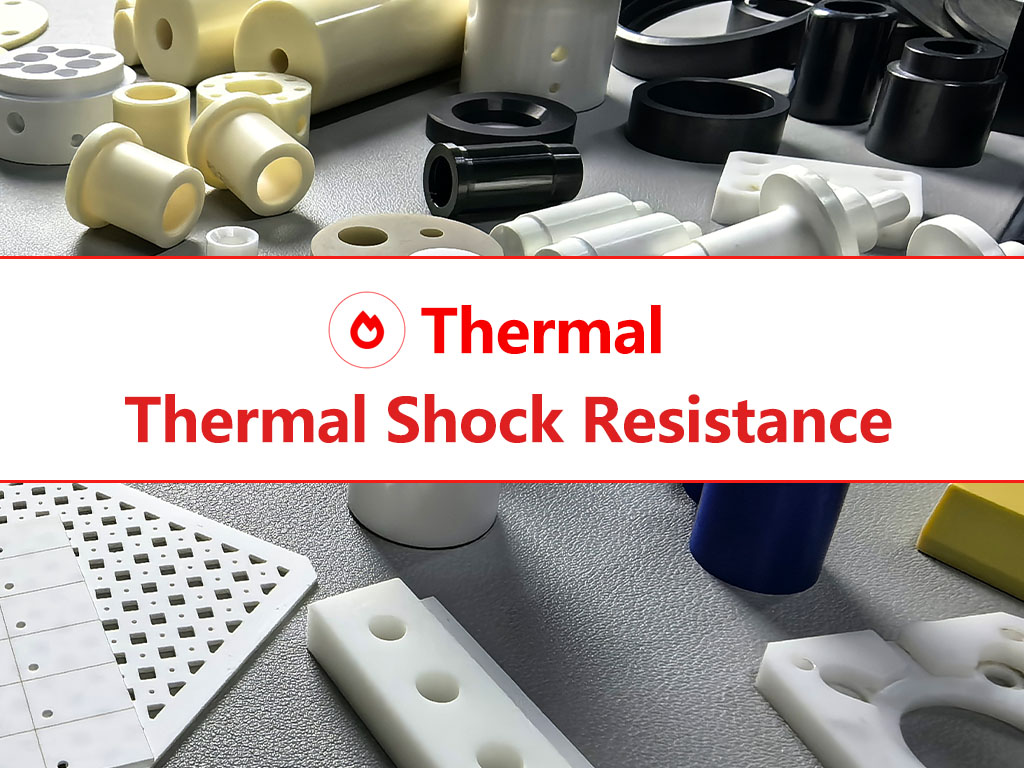
Why Thermal Shock Resistance Matters for Ceramics
Ceramics often operate in environments where temperature changes are extreme and unpredictable:
Without proper thermal shock resistance, even high-strength ceramics can fail suddenly, leading to equipment damage, safety risks, and increased maintenance costs.
Influencing factors
Conclusion: Materials with lower thermal expansion and higher thermal conductivity usually exhibit better thermal shock resistance.
Design principles
Thermal shock resistance Data of Key Advanced Ceramics
Choosing the right advanced ceramic for thermal shock conditions requires balancing mechanical strength, thermal expansion, and thermal conductivity. While no single material excels at everything, tailored selection allows for optimal performance under thermal cycling stress.
At Great Ceramic, we provide material recommendations and precision machining for various thermal applications, from aerospace to semiconductor industries.
Material | Thermal conductivity(W/m·K) | Thermal Expansion (10⁻⁶/K) | Typical ΔT Tolerance(℃) | Characteristics |
---|---|---|---|---|
Silicon Nitride (Si₃N₄) | 20–30 | 2.8–3.3 | 500~700 | High fracture toughness + medium to high thermal conductivity, the preferred material for thermal shock |
Silicon Carbide (SiC) | 120 | 4.0–4.5 | 350~500 | High thermal conductivity + high strength, widely used in metallurgical and chemical thermal environments |
Aluminum Nitride (AlN) | 175 | 4.5–5.3 | 300~500 | High thermal conductivity ceramics, widely used in thermal management systems |
Beryllium Oxide (BeO) | 230 | 7.5–9.0 | ~250 | Ultra-high thermal conductivity, but toxic, limited use |
Zirconia Toughened Alumina | ~15 | 7.5–8.0 | ~325 | Toughened alumina, suitable for mild thermal shock environment |
Boron Nitride (BN) | 60–80 (hex) | 1.0–2.0 | ~200 | Very low expansion coefficient but low strength, suitable for thermal insulation interface |
Machinable Glass Ceramic | 1.5–3.5 | 3.0–3.5 | ~200 | Good machinability, but low thermal conductivity and strength |
Zirconia (ZrO₂) | 2.5–3 | 10.0–11.5 | ~300 | High toughness but low thermal conductivity, prone to cracking due to sudden temperature changes |
Alumina (Al₂O₃, 99.5%) | 25–35 | 7.5–8.5 | 200~300 | Commonly used ceramics, but not suitable for frequent thermal shock environments |
*Data is for reference only.
Need Help Choosing the Right Ceramic?
Selecting the right high thermal shock resistant ceramic material is critical to ensuring long-term reliability and optimal performance. Whether you require silicon nitride, aluminum nitride or silicon carbide ceramic materials, our materials offer industry-leading performance, durability and precision.
Our technical team is here to help – contact us today for expert, customized advice based on your specific needs.
Comparison: Ceramics vs Metals and Plastics
The following bar chart ranks common materials by their approximate thermal shock resistance values, using the R-parameter as an indicator (higher = better). These values are derived from material databases and industry benchmarks.
■ Red: Advanced Ceramics ■ Yellow: Metals ■ Green: Plastics
*Data is for reference only.