Comparison of three common ceramic substrates
Ceramic substrates are widely used in various high-performance applications due to their excellent mechanical, thermal, and electrical properties. Among them, aluminum nitride (AlN), 96% alumina (Al₂O₃), and silicon nitride (Si₃N₄) ceramic substrates are the most commonly used materials in electronics, aerospace, and power devices. This article provides a comprehensive comparison of their performance, characteristics, and applications, helping engineers and designers select the right ceramic substrate for their needs.
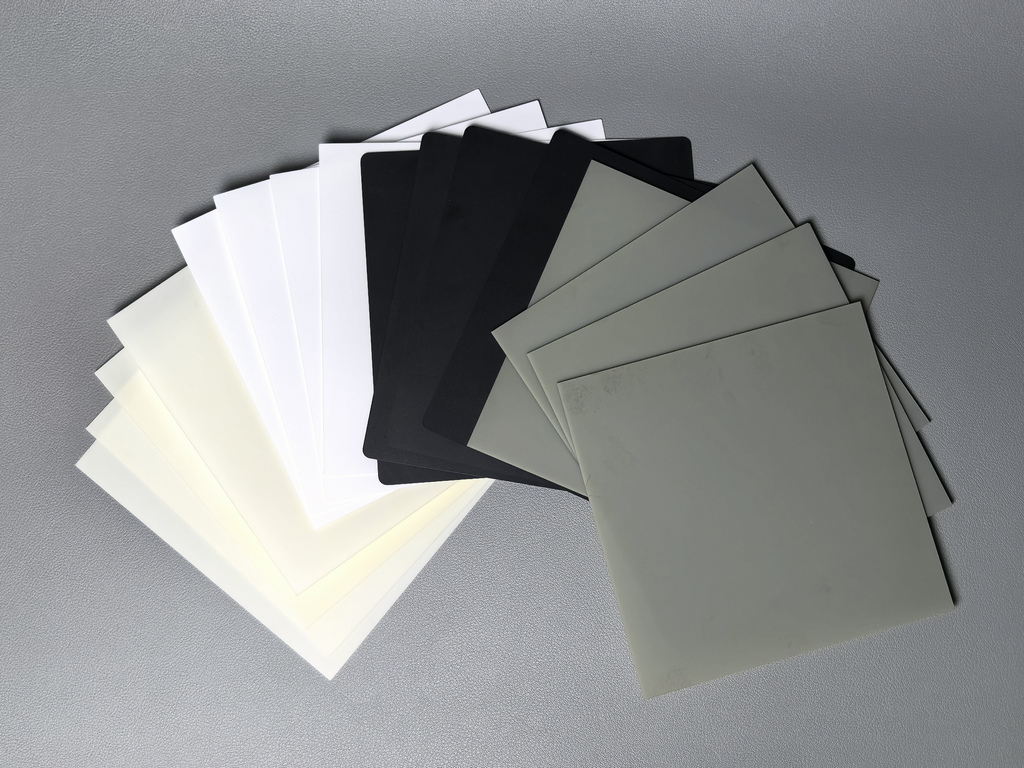
Mechanical Properties Comparison
Ceramic substrates must withstand mechanical stresses in various environments, making flexural strength, hardness, and fracture toughness critical factors.
Property | Aluminum Nitride (AlN) | 96% Alumina (Al₂O₃) | Silicon Nitride (Si₃N₄) |
---|---|---|---|
Flexural Strength (MPa) | 350 | 350 | 800 (Superior) |
Hardness (HV) | 1150 | 1600 (Hardest) | 1500 |
Fracture Toughness (MPa·m¹/²) | 4.0 | 3.2 | 7.0 (Best for impact resistance) |
Thermal Properties Comparison
Thermal conductivity and expansion are crucial for heat dissipation and thermal stability in electronic applications.
Property | Aluminum Nitride (AlN) | 96% Alumina (Al₂O₃) | Silicon Nitride (Si₃N₄) |
---|---|---|---|
Thermal Conductivity (W/m·K) | 170 (Excellent) | 22 | 25 |
Thermal Expansion (×10⁻⁶/K) | 5.0 | 7.0 | 3.0 (Lowest) |
Maximum Operating Temperature (℃) | 1000 | 1500(Highest) | 1200 |
Electrical Properties Comparison
Electrical insulation and dielectric properties affect the performance of circuit boards and semiconductor components.
Property | Aluminum Nitride (AlN) | 96% Alumina (Al₂O₃) | Silicon Nitride (Si₃N₄) |
---|---|---|---|
Dielectric Constant | 8.8 | 9.5 | 8.2 |
Dielectric Loss (×10⁻³) | 2.0 | 3.0 | 1.5 (Lowest) |
Volume Resistivity (Ω·cm) | 10¹³ | 10¹⁴ (Best Insulation) | 10¹² |
Main performance comparison
Below is a comparison chart of the main properties of the three ceramic substrates, which can quickly see the differences in each performance.
Applications of Ceramic Substrates
Based on their properties, each ceramic substrate excels in different industries:
Aluminum Nitride (AlN) Ceramic Substrate
96% Alumina (Al₂O₃) Ceramic Substrate
Silicon Nitride (Si₃N₄) Ceramic Substrate
Comparison of main uses of ceramic substrates
Application Areas | Aluminum Nitride (AlN) | 96% Alumina (Al₂O₃) | Silicon Nitride (Si₃N₄) |
---|---|---|---|
Power Electronic Modules | ⭐⭐⭐⭐⭐ (Excellent, due to high thermal conductivity) | ⭐⭐ (Poor thermal conductivity) | ⭐⭐⭐⭐ (better, impact-resistant) |
LED Packaging Substrates | ⭐⭐⭐⭐⭐ (High thermal conductivity) | ⭐⭐ (Poor thermal conductivity) | ⭐⭐⭐ (good impact resistance) |
RF/Microwave Substrates | ⭐⭐⭐⭐⭐ (low dielectric loss) | ⭐⭐⭐ (General application) | ⭐⭐⭐⭐ (High reliability) |
IC Packaging Substrates | ⭐⭐⭐⭐⭐ (thermal expansion matching silicon) | ⭐⭐ (Thermal expansion mismatch) | ⭐⭐⭐⭐ (High reliability) |
Aerospace | ⭐⭐⭐⭐ (High performance application) | ⭐⭐⭐ (generally heat resistant) | ⭐⭐⭐⭐⭐ (impact resistant, high temperature resistant) |
Automotive Electronics | ⭐⭐⭐⭐ (high heat dissipation, some applications) | ⭐⭐⭐ (low cost, common) | ⭐⭐⭐⭐⭐ (impact resistant, high temperature resistant) |
Industrial Heating Substrates | ⭐⭐⭐⭐ (high temperature resistant) | ⭐⭐⭐⭐⭐ (high temperature resistance, low cost) | ⭐⭐⭐⭐⭐ (extremely high heat resistance) |
Conclusion: Which Ceramic Substrate Should You Choose?
By understanding the performance differences among AlN, Al₂O₃, and Si₃N₄ ceramic substrates, engineers and manufacturers can optimize material selection for enhanced performance and longevity.
For customized precision ceramic substrates, visit Great Ceramic and explore our advanced technical ceramics!