What Are Advanced Technical Ceramics?
Advanced ceramics, also known as technical ceramics, engineering ceramics, or high-performance ceramics, are specialized inorganic materials designed for extreme operating conditions. They offer superior mechanical strength, thermal stability, wear resistance, and electrical insulation compared to traditional ceramics, making them indispensable in high-tech and industrial applications.
Why use advanced ceramics?
Due to their remarkable high-temperature capabilities, hardness and electrical properties, advanced technical ceramics are often used to replace metals, polymers and refractories. When used properly, ceramics can extend product life, increase efficiency, reduce overall maintenance costs and improve product performance.
Advantages of Advanced Ceramics
Advanced ceramics possess a unique combination of properties that provide clear advantages over metals and polymers in demanding technical applications:
Limitations of Advanced Ceramics
Despite their many strengths, technical ceramics also present certain limitations that must be considered:
Ceramics vs. Metals vs. Plastics: Performance Comparison
Property | Advanced Ceramics | Metals (e.g., Steel, Al) | Plastics (e.g., PEEK, PTFE) |
Hardness (HV) | 1000 – 2500 | 100 – 700 | 10 – 30 |
Max Operating Temp (°C) | 800 – 1800 | 200 – 1000 | 80 – 300 |
Electrical Resistivity (Ω·cm) | >10¹² | <10⁻⁵ | >10¹⁵ |
Thermal Conductivity (W/m·K) | 1.5 – 300 | 50 – 400 | 0.2 – 0.4 |
Corrosion Resistance | Excellent | Moderate to poor | Moderate |
Machinability | Poor (after sintering) | Excellent | Excellent |
Toughness (MPa·m½) | 2 – 10 | 20 – 100 | 3 – 5 |
Density (g/cm³) | 2.2 – 6.1 | 2.7 – 8.9 | 0.9 – 2.2 |
Summary: Ceramics outperform metals and plastics in harsh environments requiring hardness, heat resistance, insulation, or chemical stability. Metals remain ideal for ductile or load-bearing applications. Plastics offer ease of fabrication but lack temperature or wear tolerance.
Advanced Ceramic Materials Comparison
Great Ceramic is a reliable ceramics supplier offering a comprehensive range of materials, each with distinct characteristics:
Material | Density | Hardness | Flexural Strength | Fracture Toughness | Max Temp | Thermal Conductivity | Electrical Resistivity | Applications |
Alumina (Al₂O₃) | 3.7–3.9 | 1500–1800 | 300–500 | 3–4 | ~1600 °C | 25–35 W/m·K | >10¹⁴ Ω·cm | Insulators, wear parts |
Zirconia (ZrO₂) | 5.6 | 1100–1300 | 800–1000 | 6–10 | ~1200 °C | 2–3 W/m·K | ~10¹³ Ω·cm | Dental, tools, bearings |
Silicon Nitride (Si₃N₄) | 3.2 | 1400–1700 | 700–950 | 6–8 | ~1400 °C | 15–30 W/m·K | >10¹³ Ω·cm | Turbines, engine parts |
Silicon Carbide (SiC) | 3.1 | 2200–2500 | 400–600 | 3–4 | 1600–1800 °C | 80–120 W/m·K | >10¹² Ω·cm | Seals, heat exchangers |
Aluminum Nitride (AlN) | 3.3 | 1100–1400 | 300–400 | 2.5–3.5 | ~1200 °C | 170–200 W/m·K | >10¹³ Ω·cm | Electronics, LED bases |
Machinable Glass Ceramic (MGC) | 2.4 | 500–600 | 150–200 | 1.5–2 | ~800 °C | 1.5–2 W/m·K | >10¹² Ω·cm | Prototypes, vacuum parts |
ZTA | 4.0–4.2 | 1400–1700 | 500–700 | 5–7 | ~1500 °C | 18–25 W/m·K | >10¹³ Ω·cm | Cutting tools, implants |
h-BN | 2.2–2.3 | ~400 | ~100–150 | ~1 | ~900–1800 °C | 30–60 W/m·K | ~10¹² Ω·cm | Lubrication, thermal interface |
Beryllia (BeO) | 2.85 | ~1100 | ~300–400 | ~2.5 | ~1400 °C | 250–300 W/m·K | >10¹³ Ω·cm | RF electronics, defense |
Material Characteristics and Applications
Each material in technical ceramics serves unique industrial needs. Below is a brief summary:
Ceramics Design Guide
To help your ceramic parts succeed in production, consider the following:
Our technical team will assist you in optimizing your part design for both function and manufacturability.
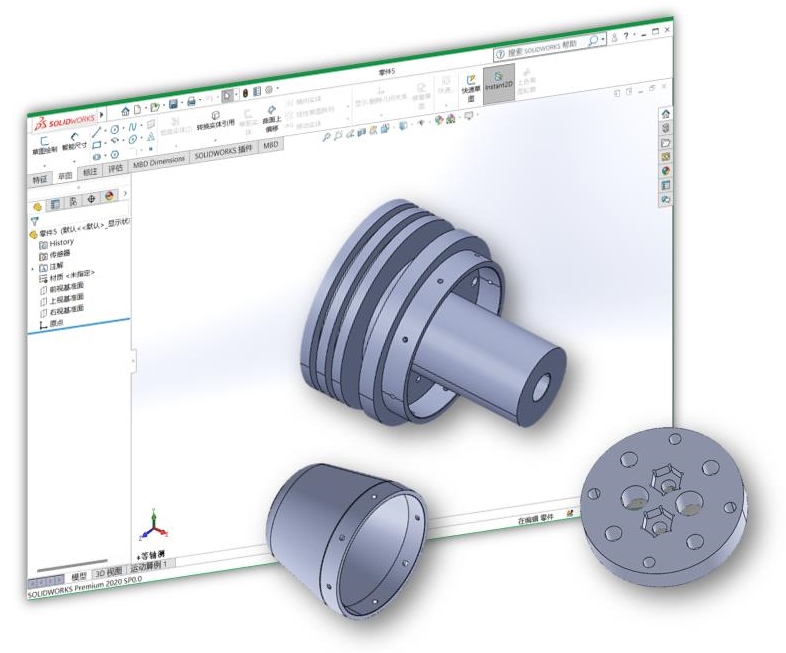
Advanced Ceramics Manufacturing & Processing
Advanced ceramics manufacturing involves:

- material configuration
- Spray granulation

- Dry pressing
- Isostatic pressing
- Injection molding
- Casting molding
- Hot isostatic pressing
- Extrusion die molding

- Sintering
- Hot pressing sintering

- CNC machining
- Grinding
- Polishing
- Laser cutting
- Surface metallization
- Welding

- ISO9001:2016
- Passed strict inspection
- Various testing equipment
Advanced ceramic machining
Advanced ceramics, such as alumina, zirconium oxide, silicon nitride, etc., are often used in high-purity and high-performance applications, with a purity of up to 99.9%. These materials have extremely high hardness and chemical stability, making traditional processing methods almost incapable after sintering.
Therefore, ceramics usually need to be formed by pressing, grouting, extrusion, etc. in the “green body” stage (before sintering). After sintering, the material will shrink by about 20% in volume, and the reserved dimensions must be accurately calculated during molding. After full sintering, the material becomes very hard and brittle and can only be ground, drilled, polished and micro-machined by diamond tools.
The processing process is extremely demanding on equipment, usually requiring multi-axis CNC machining centers and dedicated cooling and lubrication systems to prevent thermal cracks or microcracks. The processing tolerance is extremely small, suitable for high-end applications that require high precision.
Although the processing cost is high, this precision ceramic processing can meet the stringent requirements of materials performance in extreme environments in industries such as electronics, aerospace, medical and semiconductors, and is a solution that cannot be replaced by metals and plastics.
Our ceramic machining capabilities
Industrial Applications of Ceramics
- Electronics: Substrates, insulators, thermal interface materials
- Automotive: Oxygen sensors, fuel components, bearing rings
- Aerospace: Thermal barriers, structural components
- Medical: Dental implants, orthopedic prostheses
- Industrial Equipment: Valves, pump liners, cutting tools
- Defense & Energy: Armor, radomes, nuclear insulators
Their adaptability makes them essential across all major high-tech sectors.
FAQs About Advanced Ceramics
Custom Ceramic Machining & Solutions
With advanced CNC equipment and decades of ceramic machining experience, Great Ceramic provides:
We support your project from material selection to final production — offering cost-effective, precision-driven ceramic manufacturing.