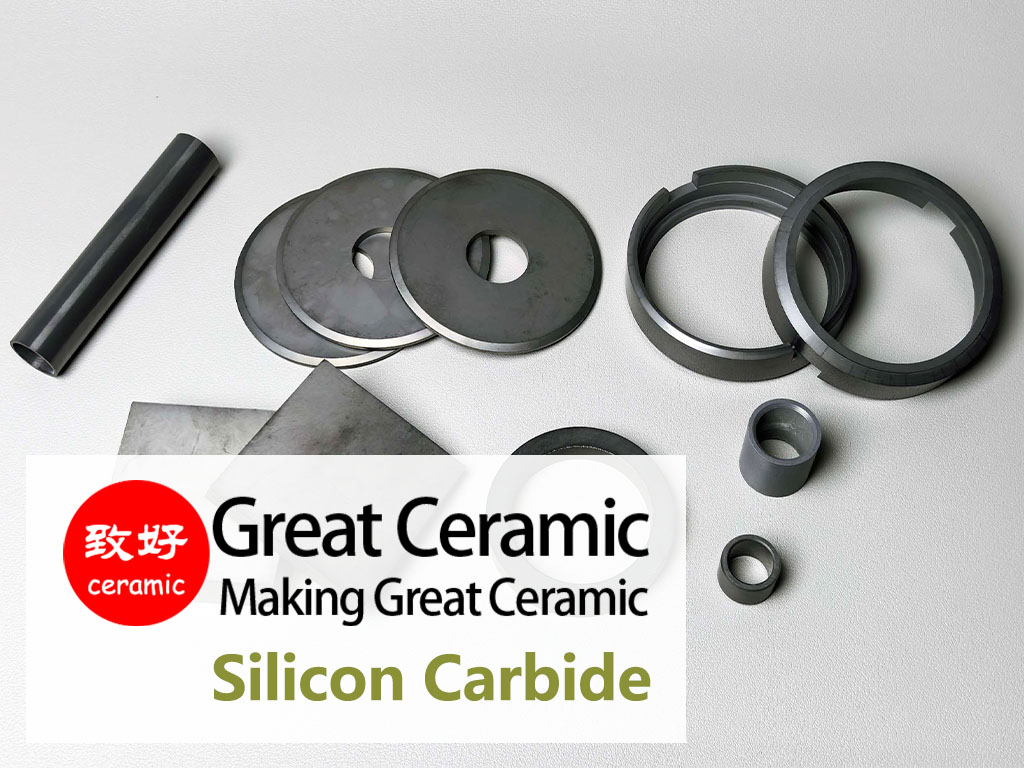
炭化ケイ素焼結方法とモデル
現在、炭化ケイ素セラミックスの焼結方法には、主にホットプレス焼結、直接焼結、反応焼結、再結晶焼結、マイクロ波焼結、スパークプラズマ焼結などがあります。焼結方法が異なれば、炭化ケイ素材料の特性も異なります。そこで、最も一般的な2つの焼結成形法を以下に簡単に紹介する。
直接焼結炭化ケイ素(SSiC)
直接焼結炭化ケイ素は、純粋な炭化ケイ素粉末と酸化物を含まない焼結助剤から、ドライプレスや押出成形を含む様々な成形方法を用いて、不活性雰囲気中、約2,000℃の高温で製造される。
反応結合炭化ケイ素(SiSiC)
反応焼結による炭化ケイ素の調製方法は、炭化ケイ素粉末に適量の炭素含有材料を予混合し、炭化ケイ素粉末中の炭素と残留ケイ素との高温反応を利用して新しい炭化ケイ素を合成し、コンパクトな構造の炭化ケイ素セラミックスを形成する。
反応焼結プロセスは、焼結温度が低い、焼結時間が短い、ネットサイズに近い成形が可能などの利点があります。大型で複雑な形状の炭化ケイ素セラミックスを製造する最も効果的な方法です。
炭化ケイ素の特性
- 密度は比較的低い;
- より高い機械的強度;
- 優れた高温強度;
- 耐酸化性;
- 優れた耐熱衝撃性;
- 高い硬度と耐摩耗性;
- 熱膨張率が低く、熱伝導率が高い;
- 優れた耐薬品性。
SiC材料の性能パラメータ
プロパティ | 単位 | SSiC | SiSiC | Si3N4 |
---|---|---|---|---|
カラー | -- | ダークグレー | ダークグレー | グレーまたはブラック |
密度 | g/cm³ | 3.15 | 3.02 | 3.2 |
多孔性 | % | ≤0.1 | ≤0.1 | -- |
硬度 | GPa | 22 | 22 | 15 |
圧縮強度 | MPa | 2600 | 2600 | 2500 |
曲げ強度 | MPa | 400 | 250 | 700 |
弾性係数 | GPa | 410 | 330 | 300 |
最高使用温度 | ℃ | 1400 | 1000 | 1100 |
熱伝導率 | W/(m・K) | 100~120 | 45(1200℃) | 15~20 |
熱膨張係数 | 1 x 10-6/°C | 4 | 4.5 | 3 |
*数値は代表的な物性値であり、製品構成や製造工程によって異なる場合があります。詳細は下記までお問い合わせください。 お問い合わせ.
炭化ケイ素材料の化学的性質
酸素反応の温度が1300℃に達すると、炭化ケイ素結晶の表面に二酸化ケイ素の保護層が形成される。保護層が厚くなることで、内部の炭化ケイ素が抵抗して結合し続けるため、炭化ケイ素結晶は良好な耐薬品性を持つ。耐食性の面では、SiC材料は二酸化ケイ素保護膜の役割により強い耐酸性を持つが、耐アルカリ性は劣る。
炭化ケイ素の用途
炭化ケイ素材料は密度が低いだけでなく、非常に高い硬度を持ち、最も硬いセラミック材料の一つである。その材料特性は、1400℃の温度でも変化しません。また、高いヤング率(400GPa以上)により、高圧下での寸法安定性が保証されている。また、毒物学的に安全であり、食品産業にも使用できる。さらに、SiC材料は熱伝導性に優れ、熱膨張率が低く、酸やアルカリに非常に強い。
- 回転ボール&ローラーベアリング
- 切削工具
- エンジン部品
- バルブ、ロッカーアームパッド、シール面
- 誘導加熱コイルサポート
- タービンブレード、ベーン、バケット
- 溶接・ろう付け治具
- ヒーティング・エレメント部品
- 固定および移動タービン部品
- シール、ベアリング、ポンプベーン
- ボールバルブ付属品
- ウェアプレート
- 窯道具
- 熱交換器
- 半導体ウェハー処理装置
炭化ケイ素構造部品
グレートセラミックでは、長年にわたって蓄積された豊富な経験、様々な洗練された加工設備、セラミック材料に関する専門的な知識をもとに、様々な炭化ケイ素構造部品のカスタマイズされた加工サービスをお客様に提供しています。
炭化ケイ素セラミックスメーカー
Great Ceramicは炭化ケイ素材料の専門メーカーです。先端セラミックにおける長年の経験を生かし、材料、設計、用途についていつでも喜んでアドバイスさせていただきます。炭化ケイ素のシート、ロッド、チューブ、またはカスタム加工された構造部品の購入をご希望の場合は、ご連絡ください。